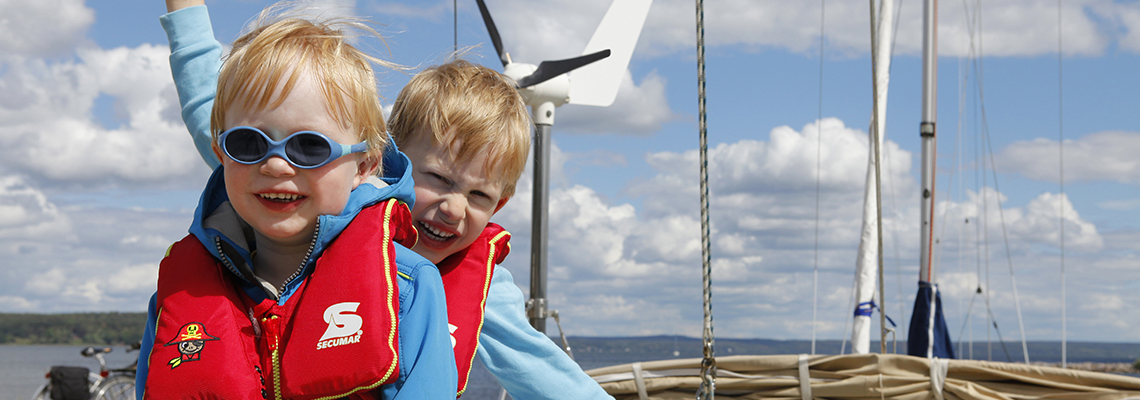
A walk through the production facility.
A picture says more than a thousand words – so we invite you to have a look over the shoulder of our production staff as they go about their business.
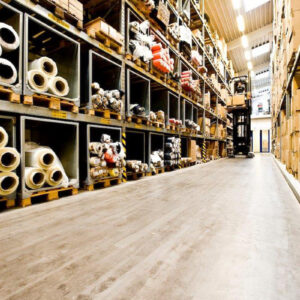
The warehouse, where all the parts and materials for the manufacture of lifejackets are checked and stored.
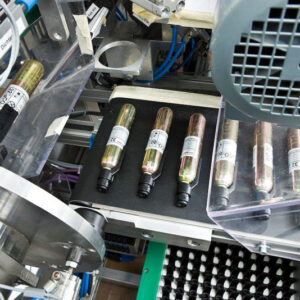
Every CO2 cylinder is automatically and individually checked before fixing it into the lifejacket firing mechanism.
Many small parts comprise the lifejacket firing mechanism. Here the manual and automatic features are being 100% quality controlled.
The finished welded swim bladders have reflective strips attached and are then test inflated for 16 hours.
The first phase of the destructive burst test. Swim bladders are inflated in a sound-proof chamber until …
Servicing: the firing mechanism is at the heart of every inflatable lifejacket – small metal discs are used to check the strength of the firing spring.